top of page
AAA Tooling Design & Manufacturing Company Limited
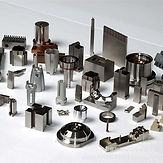

Lower Your Cost Now
-
WHAT TOLERANCES CAN YOU ACHIEVE?There is not a given set of tolerances that fits all processes and materials. In every case, the final tolerances on your part will depend on a number of factors, including but not limited to:Part sizeDesign geometryThe number, type and size of featuresMaterial(s)Surface finishManufacturing processWe will review your design and provide a design for manufacturing review, pointing out any areas where we may not be able to achieve your desired tolerances. It’s helpful to us if you can specify which areas in your design have critical tolerances that must be met and which can be slightly modified if needed to reduce time and costs involved.
-
HOW DO YOU ENSURE YOUR QUALITY?In order to deliver high-quality parts every time, we’ve instituted the following steps to ensure you get parts that meet and exceed your expectations. A full design for manufacturing (DFM) review upon initial inquiry. This will be performed by our skilled engineering team, who will alert you to any issues before work begins. All incoming material (metal and plastic) is 100% inspected using our in-house metrology equipment. This includes OES, XRF and PolyMax spectroscopy. In-process and first article inspection. Comprehensive final inspection with full report.
-
HOW DO I KNOW MY DEISGN WILL BE KEPT CONFIDENTAIL?First, we allow no photographs to be taken of your product or tooling without your express, written permission. No documentary information related to a customer’s product is allowed to leave the confines of the physical office, either in printed or electronic form, with the following exception: should it be necessary to perform some process on a customer’s part using an outside, third-party vendor, then the customer’s identifying information shall be removed from all relevant documentation. The outside vendor shall receive only that information necessary to their performance of the sub-contracted work. If we expect a breach of internal computer security, all transactions on all computers are automatically backed-up, 24/7, on secure servers in cHINA and can be traced back to individual user accounts if necessary. We will sign and abide by all NDAs to the limits of our ability. Ultimately, however, perfect security is not possible for ourselves or for any company, anywhere. In the vast majority of cases we don’t have access to the product in its final form, especially if it contains electronics and control software – often the very heart of proprietary information. It is in our long-term interest to maintain the highest level of trust with our customers. Should there ever be a case of missing or stolen data, we will work with you to pursue the matter to the limits of the law. Our reputation depends on it.
-
WHAT IF WE ARE NOT COMPLETELY SATISFIED WITH THE PARTS WE RECEIVED?If it is practical to do so, we will replace free of charge any parts that you are not completely satisfied with. If that is not practical, then we will credit the customer a negotiated sum. Regarding plastic injection molded and pressure die cast samples: T1 (first trial of tooling) samples are never completely satisfactory, this is an industry norm. For example, T1 samples rarely carry the final finish/texture as the customer often finds the need to modify the design and have tooling changes made.
bottom of page